造成鍍層裂紋的原因在于噴焊前工件的預(yù)熱溫度太低和重熔后冷卻速度太快,噴焊層與基體金屬的膨脹系數(shù)相差太大,以及基材金屬冷卻時(shí)出現(xiàn)較大的相變所引起的應(yīng)力等等,主要原因有下述幾個(gè)方面。1、噴鍍時(shí),噴槍移動(dòng)太慢或太近,以致一次噴鍍的鍍層過厚,造成鍍層過熱,導(dǎo)致鍍層氧化嚴(yán)重。2、噴鍍材料收縮率太高或含有較多的導(dǎo)致熱裂冷碎的元素,如:硫、磷等。3、工件噴鍍結(jié)束后,如冷卻速度過快,會(huì)引起應(yīng)力。
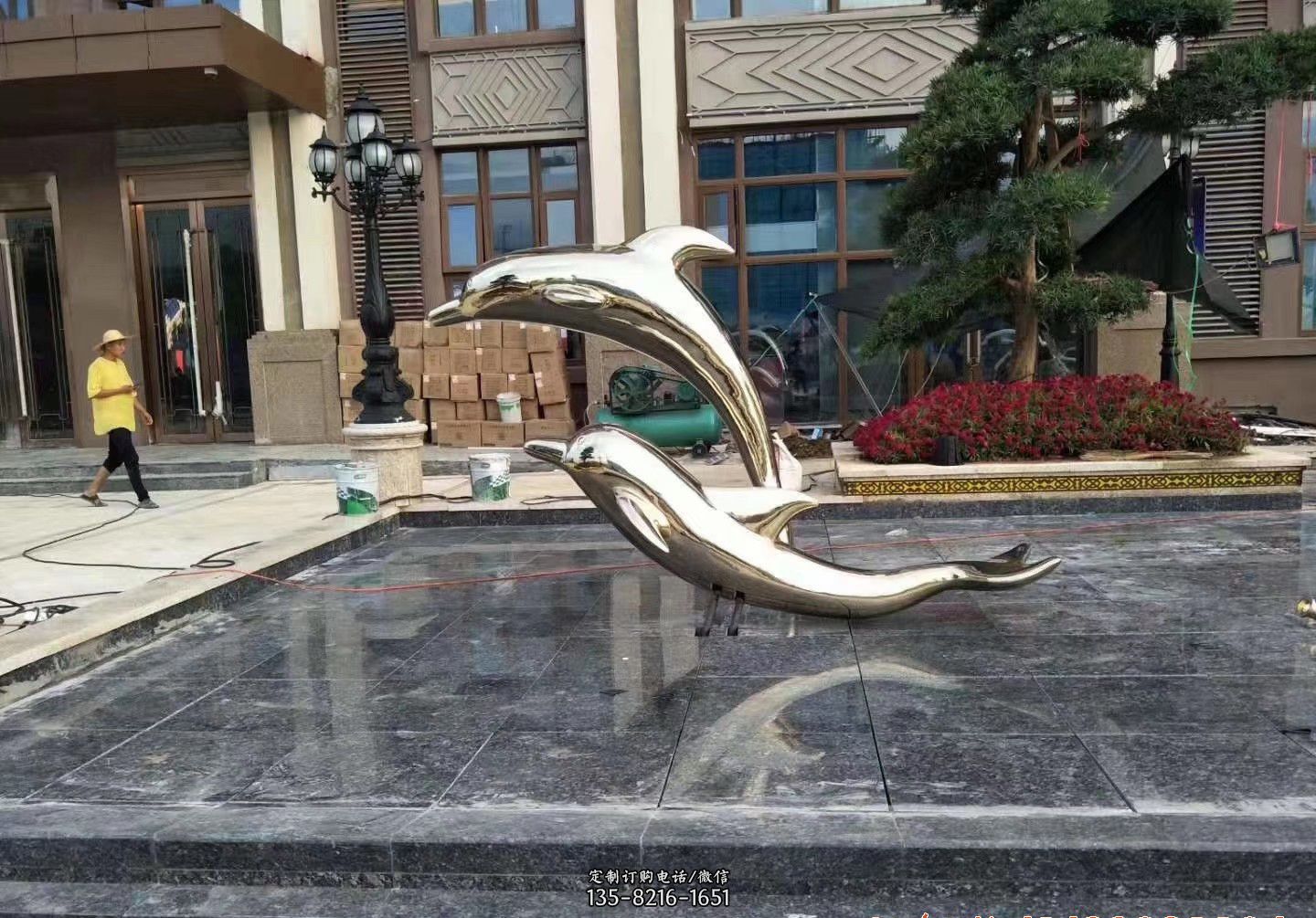
4、壓縮空氣中有水和油霧,降低了鍍層的結(jié)合強(qiáng)度。5、工件轉(zhuǎn)動(dòng)中心不準(zhǔn),噴鍍火花偏斜在一面,使鍍層有厚薄,收縮率不均勻。這些不良的因素都可能會(huì)使鍍層出現(xiàn)碎裂的現(xiàn)象。在機(jī)械加工過程中,如果鍍層與基體結(jié)合不良,往往會(huì)造成鍍層脫殼。
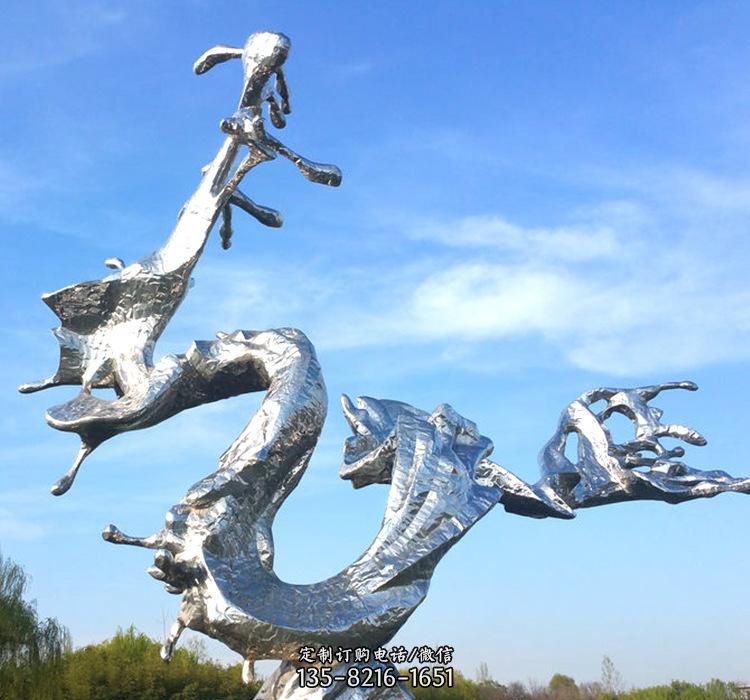
歸納起來主要有以下幾方面的原因。1、工件毛糙程度不夠或有灰塵吸附,使工件表面的附著力降低。2、工件含有油脂,噴鍍時(shí)油脂溢出,特別是球墨鑄鐵曲軸。3、壓縮空氣中有可見的油和水,使工件表面的附著力降低。4、噴槍離工件表面太遠(yuǎn)。當(dāng)金屬微粒到達(dá)工件表面前塑性降低,微粒與工件表面未能充分嵌合。
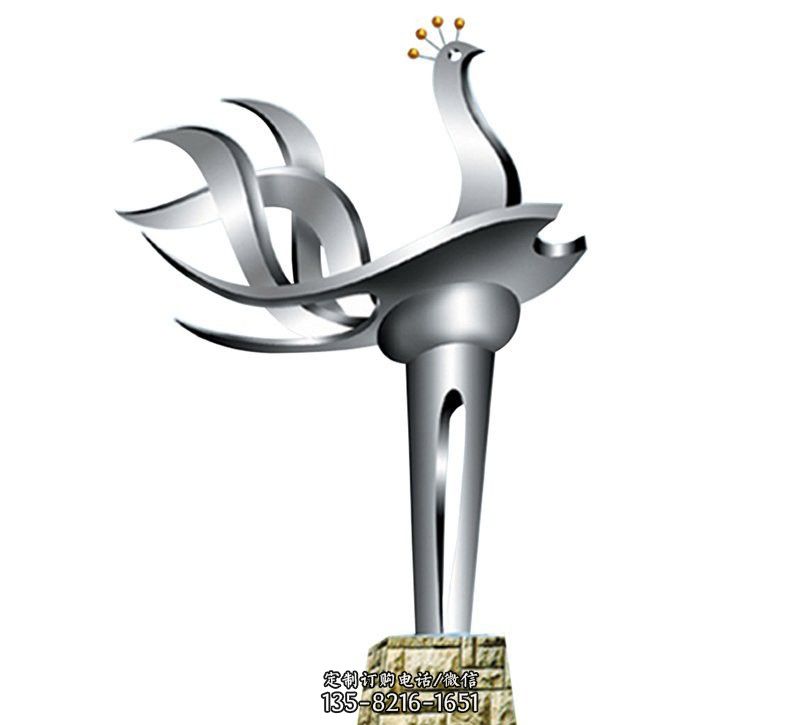
5、車削與拉毛、拉毛與噴鍍各道工序間相隔時(shí)間太久,致使表面氧化。6、噴槍火花不集中,噴鍍時(shí)火焰偏斜,致使金屬微粒不能有力地粘附在工件的表面。7、工件線速度和噴槍移動(dòng)太慢,噴鍍中的夾渣物浮于工件表面,降低了工件表面的附著強(qiáng)度。8、若工件較大,在重熔時(shí)由于溫度上升慢,致使鍍層處于高溫下長時(shí)間加熱,都會(huì)使噴焊層與基體不能良好地結(jié)合,加工時(shí)鍍層就會(huì)產(chǎn)生脫殼現(xiàn)象。
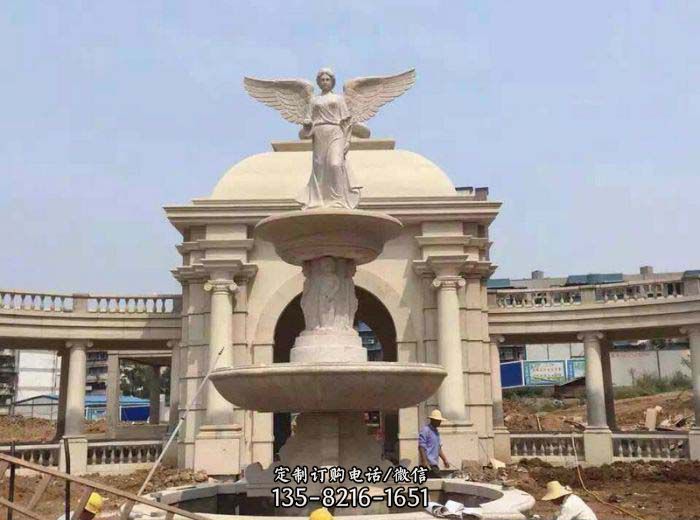
由于重熔速度過快,熔渣未能完全浮出,在焊層凝固造成夾渣。噴焊層的夾渣大多數(shù)是硼硅酸鹽類。因此,在操作時(shí)要特別注意將渣剔除。合金粉末的性能和質(zhì)量對噴焊層會(huì)產(chǎn)生夾渣也有很大的影響。如果粉末的自熔性差、熔點(diǎn)高、粘度大,就容易造成夾渣。
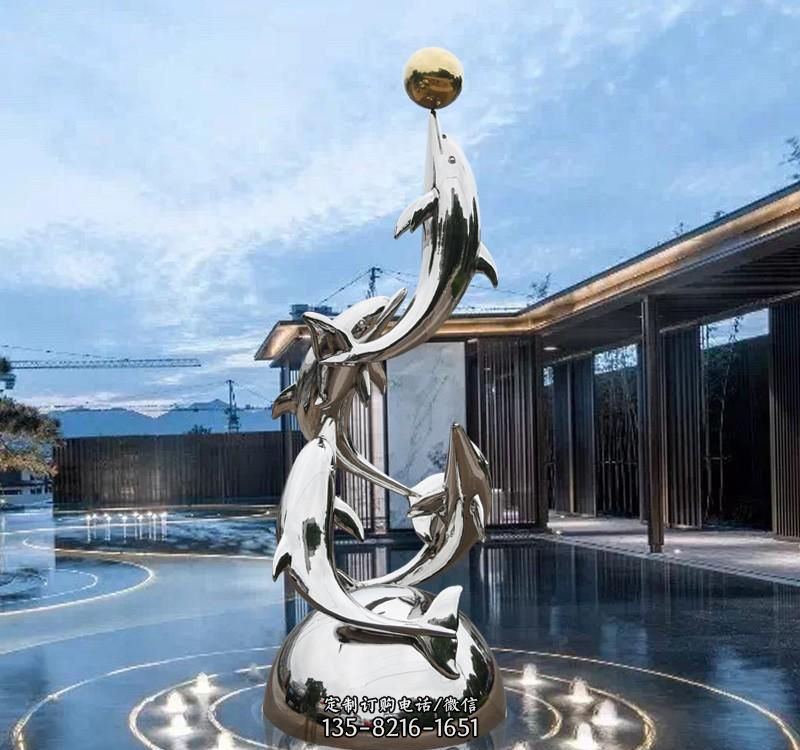
在噴鍍過程中,有時(shí)會(huì)在噴鍍層中出現(xiàn)層與層之間脫皮的現(xiàn)象。發(fā)生這種現(xiàn)象的主要原因有以下幾種。1、采用間隙噴鍍時(shí),在即將到標(biāo)準(zhǔn)尺寸的情況下沒有一次噴完,而是停噴太久。這樣完成的鍍層,在車削和磨光時(shí)就會(huì)產(chǎn)生分層剝落現(xiàn)象。2、在噴鍍過程中,由壓縮空氣帶出的油和水濺在工作表面上,使層與層之間的附著力降低。3、噴鍍場所不清潔,每一層鍍層后有大量灰塵吸附到工作表面,使得層與層之間有外來物隔離或部分隔離。在對鍍層進(jìn)行磨削時(shí),經(jīng)常會(huì)出現(xiàn)有的鍍層表面不堅(jiān)硬,部分顆粒脫落影響了泵軸的使用。
這主要是由于下列原因所造成的。1、噴鍍時(shí)噴槍離工件物太遠(yuǎn)金屬顆粒提早冷卻,噴到工件上后,成為疏松鍍層。鍍層工件時(shí)部分顆粒脫落,擦傷磨擦面。2、金屬絲進(jìn)給速度太快,顆粒呈片狀。3、金屬絲材料不合適,硬度不高,不耐磨。4、空氣壓力過低,噴距工件太遠(yuǎn)。